Linear Motor Stage
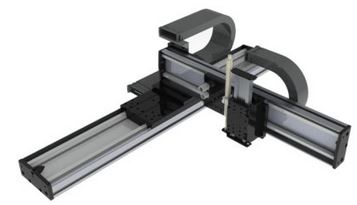
MLE Linear Motor Stages for A Repeatability of ±10µm
The MLE family of linear motor axes enables a repeatability of ±10µm through rigid linear guides and mechanics and a corresponding position measuring system. The built-in linear motor has an iron core and therefore has some cogging torque, but thanks to the iron core in the winding it offers a lot of power. See below, our MLU series for zero cogging linear motor stages for precision applications.
- MLE3 series: peak forces from 105 to 420N
- MLE5 series: peak forces from 400 to 1,600N
- MLE7 series: peak forces from 1,600 to 4,000N

MLL Linear Motor Stages for A Repeatability of ±100µm
As a low-cost variant for applications with lower requirements on repeatability, we offer the MLL family, a new series of price-optimized linear motor stages. The stroke lengths of up to 2000 mm are comparable in price with traditional solutions, such as belt-driven linear units or spindle-driven linear units. This means that you have the possibility to integrate a direct drive technology into your machine at similar prices.
Most important features:
- Continuous forces up to 600N, peak forces up to 1200N
- Position measuring system with resolution ±30 µm
- Repeatability of the stage ±100µm
- Acceleration 80 m/s2, speed up to 2 - 3 m/s
- Maximum length 4m/ axis
- Units stackable
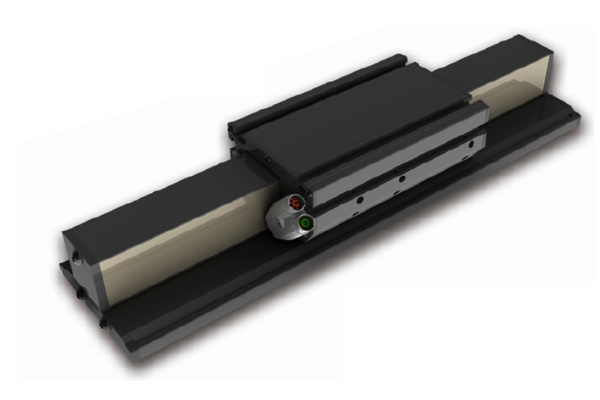
Do you have technical questions or need a quote?
MLU Stages for Zero Cogging (Ironless Motors)
Our linear motor stages of the MLU series consist of an ironless linear motor, linear guides and bearings and an integrated encoder system. The MLU linear motor stages offer peak forces up to 400N. The coil part of the linear motor is ironless (i.e. has no iron core). This means that although the motor has less force than the MLE or MLL families, it can drive and accelerate considerably faster. This makes the MLU family well suited for applications with high dynamics. A further advantage: ironless linear motors have no cogging force. Cogging force is created by the fact that the iron core of a linear motor experiences an attractive force from the permanent magnets (in the magnetic track). Ironless motors have no iron core and are therefore free of cogging torque. Zero cogging torque is a great advantage in applications where either high speed smoothness is required or where extremely low speed is required.
Overview of the main features of the MLU family:
- Repeatability of linear encoder: ± 1 μm
- Repeatability of linear stage: ± 10 μm
- Maximum speed: 9 m/s
- Maximum acceleration: 200 m/s2
- Maximum length without separation points: up to 1,000 mm
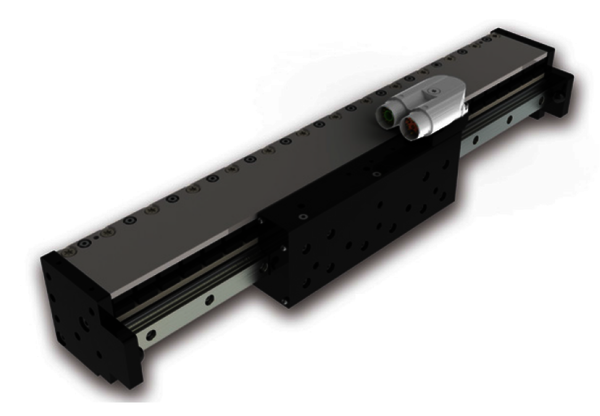
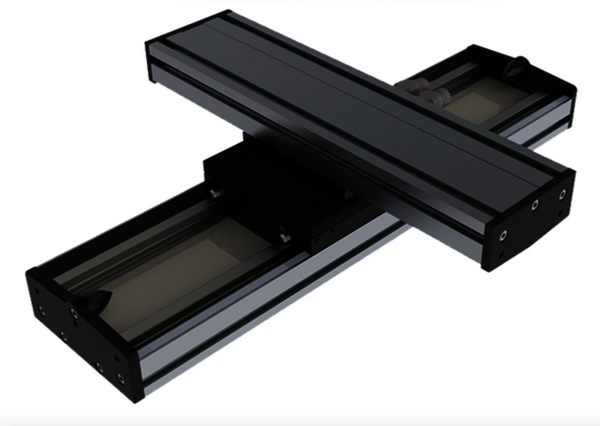
The Linear Motor Axes Can Be Combined To Various Handling Systems
- Gantry
- Portal
- Cross table
- XYZ Robot
- Cartesian robot
- 4-axis system etc.
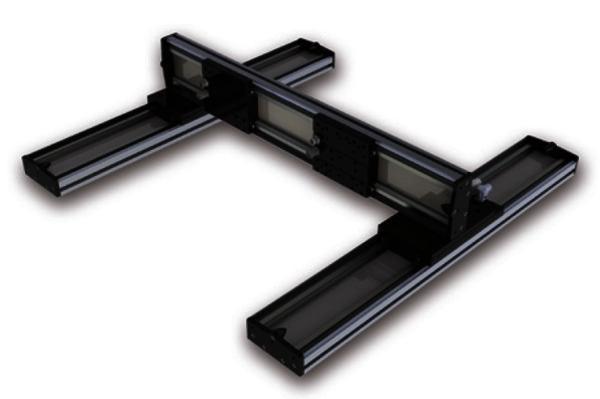
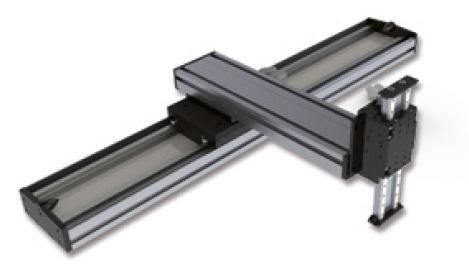
Anti-fall-protection and Brakes for Vertical Linear Motor Axes
- Pneumatic brake: in pneumatic brake, the build-up of braking force is generated with compressed air.
- Electromechanical brake: In electromechanical brakes, the braking force is generated by the motor and the chassis directly at the brake caliper by means of electricity.
- Weight compensator: A weight compensator works similarly to a pneumatic brake with compressed air. The compensator prevents the load from falling uncontrollably.
- Magnetic compensator: With a magnetic compensator, the force acts constantly over the entire length. The compensator prevents the load from falling freely in the event of a malfunction.
Do you have technical questions or need a quote?
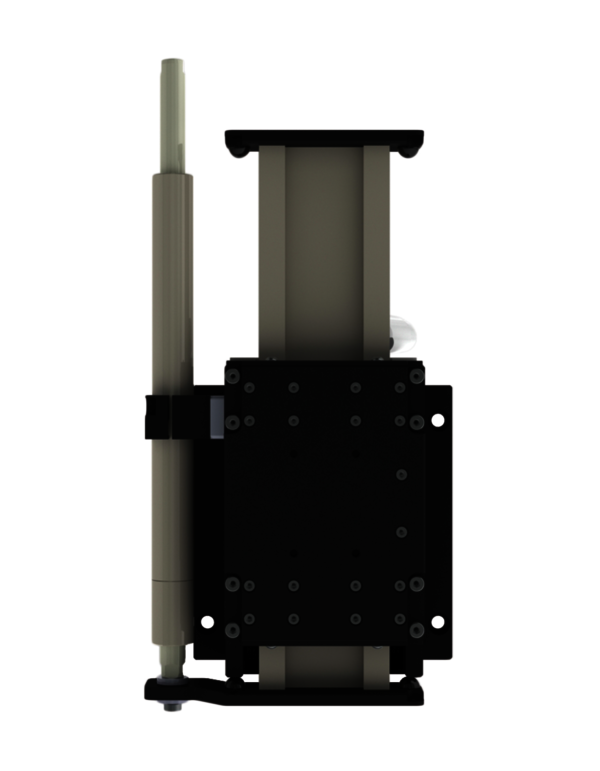
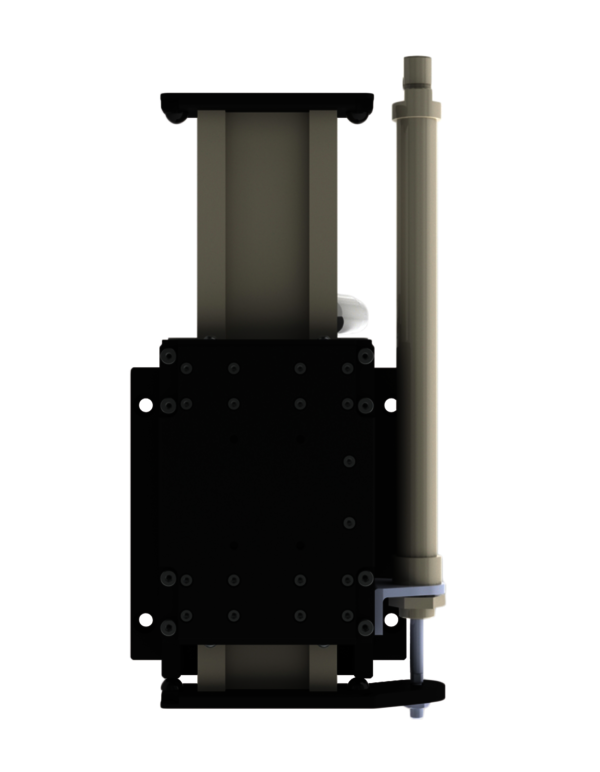
Control of Linear Motors for High-precision Applications.
For tasks such as positioning with micrometer or nanometer accuracy, or for tasks such as travel at very low speed, freedom from cogging force is a must for linear motors. However, this is by far not enough to achieve the task objective. Further requirements are: a high-resolution position measuring system and a linear servo amplifier (i.e. a non-switching servo amplifier or servo controller or servo inverter). In the field of high-resolution linear encoders we offer optical systems. You can find an overview of them under this
It is precisely this ripple that makes it more difficult to successfully commission demanding servo tasks such as positioning with micrometer or nanometer accuracy, or for tasks such as travel at very low speed. The last and perhaps most important factor for success is the experience of a commissioning engineer who has often commissioned such complex systems. RECKONIC offers exactly such engineering services. With our wealth of experience, we have helped many customers in the semiconductor, optical, laser and space industries to success. Contact us to discuss your technical requirements with an experienced engineer!
Motivation to Use Linear Motor Stages
The aim of our linear motor axes is to make the work of technicians and engineers easier and to supply a complete stage with linear guides, linear motor, encoder, connectors, limit switches and a cable drag chain. Direct-driven linear stages can score points with numerous advantages - for example, they have a much better efficiency, a higher overload capacity and better cost efficiency compared to classic axes (e.g. spindle and toothbelt axes). There are no protruding motors and gears. Our MLL, MLE and MLU series are also compatible with the most common servo control amplifiers. This allows you to use your familiar servo amplifier and thus achieve faster commissioning.
Do you have technical questions or need a quote?
Wireless Energy Transfer
For extreme conditions such as clean rooms or explosion-proof rooms, cables and drag chains are not allowed, so the electrical energy must be transmitted to the motor coil by other means. Another reason could also be: extremely high accelerations or space restrictions that preclude cable feed. For such cases, we offer special linear motor axes based on wireless power transmission. These are:
- Energy transmission via sliding contact or
- Inductive energy transfer
Energy Transfer Via Sliding Contact
In this variant, the electrical energy is transmitted via sliding contact. Such sliding contacts usually have a lifetime performance of approx. 20,000 km. The servocontroller is mounted on the linear motor carriage, together with the encoder read head. This gives the servocontroller a direct connection to the encoder read head. The commanded values are sent to the servocontroller via "Wireless CANopen" (CANopen fieldbus via Bluetooth). This means that the linear motor stage does not need a power cable or a feedback cable. This also eliminates the need for cable dragging and the associated space requirements.
Inductive Energy Transfer
Inductive energy transfer has the advantage that the lifetime performance is not limited by wear-and-tear of sliding contacts. This solution is also suitable for applications under extreme conditions such as in clean rooms or explosion-proof areas. In contrast to energy transmission via sliding contact: with inductive energy transmission, there is no dust caused by mechanical abrasion between brush and electrical track.
As before, both the servocontroller and the encoder read head can be mounted on the slide of the linear motor. The commanded values are sent via "Wireless CANopen" (CANopen fieldbus via Bluetooth). This means that the linear motor stage does not need a power cable or a feedback cable.
RECKONIC conducts research and development on the subject of high-frequency inductive power transmission. The goal: to develop an inductive receiver coil with a significantly higher power density than previously possible. The high power density requires the use of significantly higher frequencies. In contrast to today's inductive energy transmission systems (apart from small power outputs, these are in the range of 20-140 kHz), working frequencies in the MHz range are necessary.
The magnetic circuits must be designed in such a way that the energy transfer is limited to the effective area and at the same time propagating waves must be prevented. We use specially designed stranded wire cables and PCB technologies with optimized geometries to reduce coil losses at high frequencies. We use power electronics with switching frequencies in the MHz range. We use power semiconductors with a large band gap to ensure the required performance at high frequencies while maintaining high efficiency
FAQ: Certified Linear Units for Clean Room Use
1. What is a cleanroom?
A cleanroom is a controlled environment with a limited number of particles per cubic meter (m3).
2. What are the advantages of obtaining a cleanroom ISO certificate?
ISO certification makes it possible to work in different sectors where the allowed number of particles per cubic meter is limited.
3. In which sectors can this type of linear unit be used?
- Pharmaceutical industry
- Food industry
- Semiconductor industry
- Assembly of sensitive components
4. Is the use of linear units with cleanroom certification expensive?
No. By paying a small cleanroom certification fee, you save the work and time of of submitting a lot of documentation and tests.
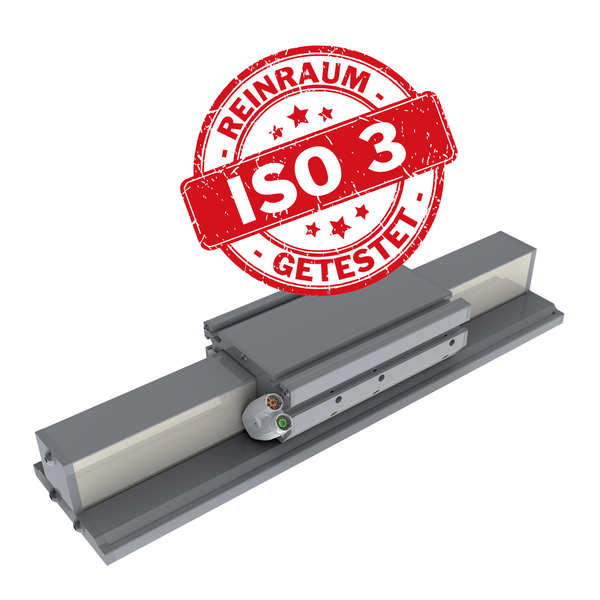