Linear Motors In Kit Form
- high speed
- high acceleration
- no or very low cogging force
- low operating noise
- high stiffness
- wear- and maintenance-free
- long travel
Do you have technical questions or need a quote?
Series of Ironless Linear Motors In Kit Form
AUM Series: Brushless, Ironless Linear Motors
Features:
- No cogging (zero cogging)
- Patented coil design for high force density
- Low intrinsic mass for high dynamics
- No magnetic attraction for interference effects
- Peak forces from 11.9N to 16,200N
- Permanent force of 3.0n to 2,340N
- Continuous forces from 3.0N to 2,340N
- Applicable up to 330VDC
- High thrust force
- High motor constant
- High motor constant
- High efficiency
- Low energy consumption
Applicable to:
- Point-to-point positioning at micrometer/nanometer level
- High/low speed applications with high speed ripple or motion profile requirements
- Precise force control
Application areas:
- Handling, testing, inspection and assembly of Wafers/LCD/PV/Batteries
- Laser processing machines
- Measuring and testing machines
- Digital printing equipment
- Metrology equipment
- Machines for DNA sequencing
- Other (bio)medical equipment
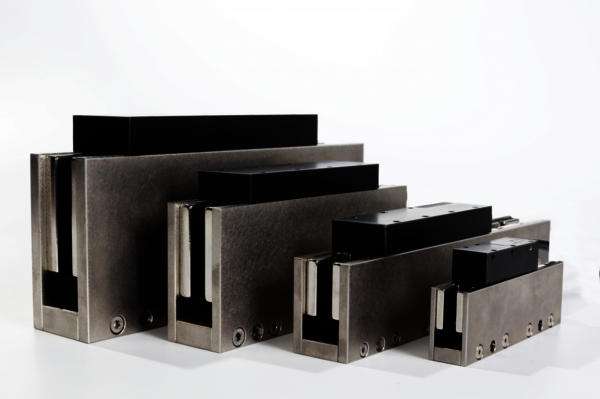
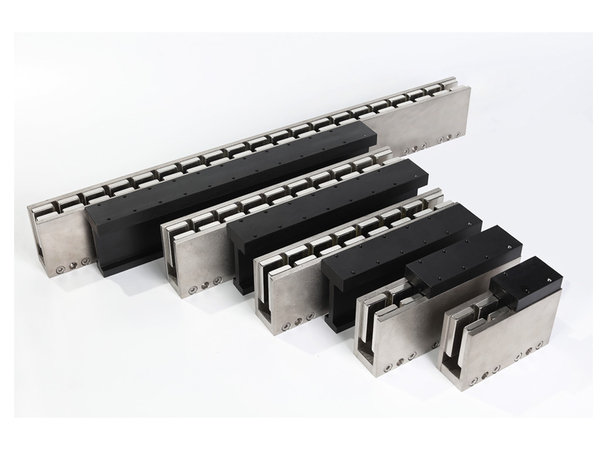
Overview of the Motor Parameters of the AUM Series
Do you have technical questions or need a quote?
ACR: Curved, Ironless Linear Motors
Features:
- No cogging force (zero cogging).
- High force density
- Low weight for high dynamics
- Large hollow shaft
- High speed for low cycle time
- Very flat design
- Configurable angle of rotation by attaching several magnetic tracks
- Flexible combination of several motors and magnetic tracks
- Applicable up to 330VDC
Applicable to:
- Point-to-point positioning at micrometer/nanometer level.
- High/low speed applications with high speed ripple or motion profile requirements
Application areas:
- Wafers/LCD/PV/Batteries
- Metrology equipment
- Laser processing machines
- Measuring and testing machines
- Digital printing equipment
- Other (bio)medical devices
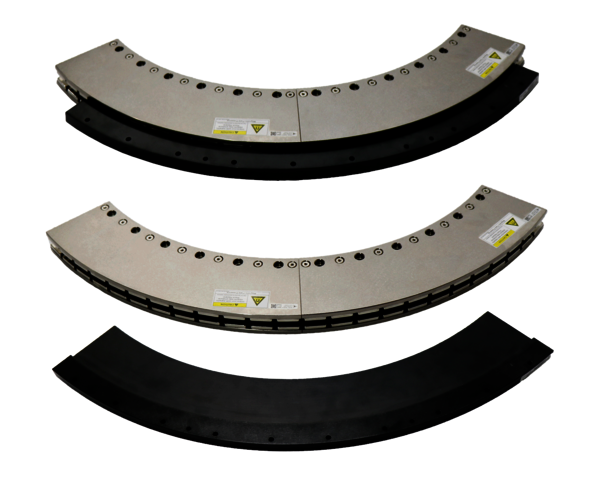
Overview of the Motor Parameters of the ACR Series
Model | Type |
Power Radius |
Height |
Coil Angel |
Continous Torque |
Peak Torque |
Datasheet |
|
ironless, frameless |
15250 |
38,8 |
|
460,7 | 1382,2 |
|
|
ironless, frameless |
240 |
33 |
|
24,3 | 72,8 | |
|
ironless, frameless |
335 |
29,6 |
|
92,3 | 276,9 | |
|
ironless, frameless |
820 |
38 |
|
331,5 | 994,5 | |
Do you have technical questions or need a quote?
Servo Control of Linear Motors for Nanometer Positioning
When control engineers contemplate difficult tasks such as micrometre / nanometre positioning, as well as aiming for speed stability at very low speeds, they usually think about several key success factors.
Firstly, eliminating cogging force or cogging torque. This is easily achieved by using ironless motors such as the ones shown on this page. In addition, it is well known that a high-resolution linear encoder system is required. This could be an optical encoder system, such as the ones shown at this link.Finally, they consider the type of servodrive which should be used. Most servodrives use pulse-width modulation of the supply voltage to achieve the required current in the motor windings. However, this leads to current ripple, which in turn produces force ripple (force produced by linear motors is proportional to current). The force ripple makes it impossible to achieve high-precision servo tasks. The solution is to use a non-switching servodrive, also known as a linear amplifier.
With the following success factors in place:- Ironless motor
- High-resolution optical encoder
- Non-switching servodrive (linear amplifier)
We can now look at the remaining puzzle pieces. Of course, we should never forget the issue of cables. High-quality motor and feedback cables which are properly shielded against electromagnetic interference are a must. Last but not least, we need an experienced commissioning engineer to get the described system working. RECKONIC has a core team of experienced engineers who have supported machine-builders in semiconductors and optics / photonics to achieve difficult nanometre positioning and low-speed motion tasks.